In order to provide better service to our customers and create a more
friendly working environment for our employees, MIT Wuhan decided to implement
5S-management throughout the production site. After nearly one month of planning,
we officially launched the 5S-project at the end of October 2019. Our idea is
to start from the welding workshop and then implement 5S gradually to other
workshops and departments. With the joint efforts of all colleagues, we have
basically completed the 5S-configuration of the welding workshop in about half
a month. At present, the welding workshop has been completely new, the tools
are well placed, the shop floor board (SFB) presents information at a glance
and the floor and walls are clean and tidy. These are only a few aspects, the
team of MIT Wuhan are proud of. We believe to complete the 5S at all workshops
and departments by the end of 2019.
.jpg?access_token=01ce8062-d550-4d0b-910b-da35dc7fa814)
welding tables area
Two of the new manual welding workplaces with shadow boards and material places (green area).
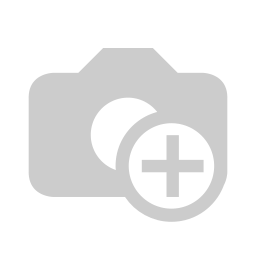.jpg?access_token=ff92da98-05db-4362-9a6a-61bd8a561e7b)
WELDING SHADOW BOARD
All welders agreed on the tools they use daily. The same boards were established for all welding tables. All other tools will be arranged in a stocking place for tools and consumables.
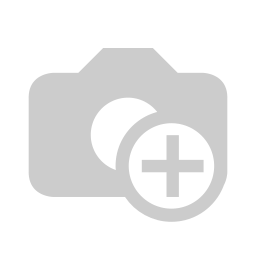.jpg?access_token=919a9c28-e000-4975-937f-9d09aa196535)
MEETING POINT
The new meeting point in the middle of the workshop contains a PC station with access to 3D-drawings and the new SHOP Floor Board, that is basis for the daily morning meeting. It contains KPI for the workshop, continuous improvement process as well as details for future work tasks.
Welding department goes LEAN!